The situation that concerns the United States is emerging, as new technologies for high-end chips are being dismantled and lithography machines may become scrap metal
Text | Jiang Zuo MeilangTypesetting Editor | Black CodeOur chip industry is facing a situation where 'a skillful woman cannot make rice without cooking'. To make high-end chips, in addition to requiring strong design capabilities, their production and processing also require extremely advanced equipment
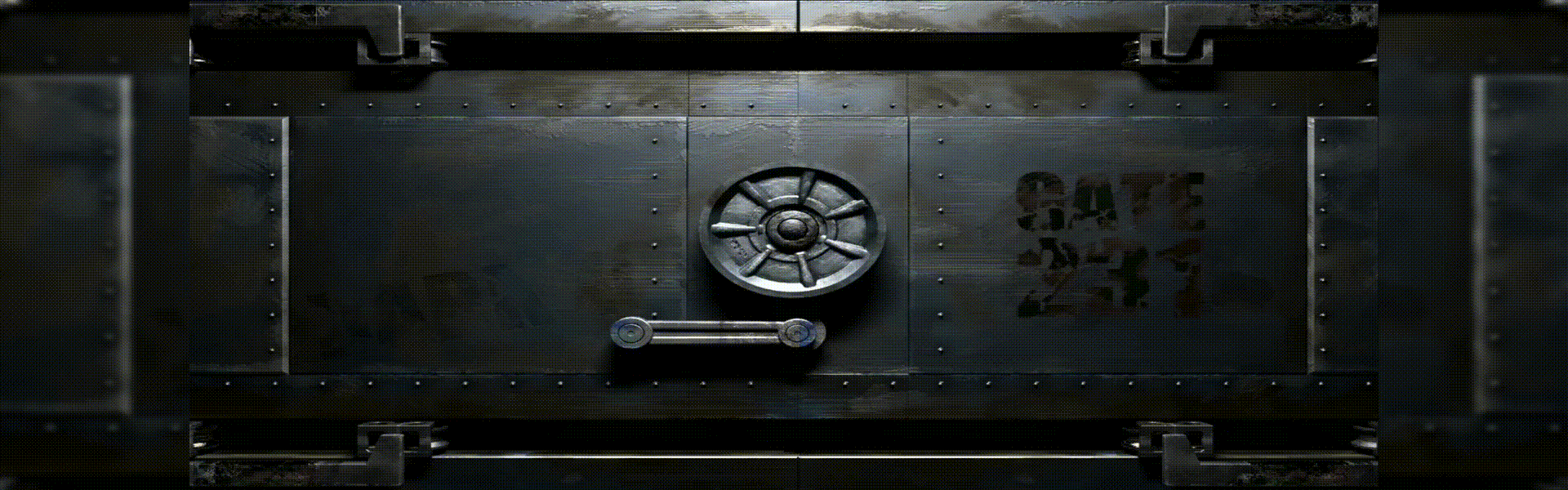
Text | Jiang Zuo Meilang
Typesetting Editor | Black Code
Our chip industry is facing a situation where 'a skillful woman cannot make rice without cooking'. To make high-end chips, in addition to requiring strong design capabilities, their production and processing also require extremely advanced equipment. Fortunately, we have overcome this in terms of design.
The problem we are facing now lies here, not only does the United States not allow ASML companies that can produce high-end lithography machines to sell equipment to us. Moreover, the high-end chips we have designed do not allow TSMC to help us produce them, and all the resources we can use have been blocked.
However, according to the current chip production process, lithography machines are a hurdle to overcome. The lithography machine, known as the pearl on the industrial crown, is the common crystallization of the world and cannot be completed by the power of a single country.

Unlike ordinary equipment, the biggest challenge of lithography machines is that the manufacturing process is difficult to keep up with the times, and high-precision equipment needs to be piled up generation by generation, because such a mechanism makes the future of high-end lithography machines lifeless.
Since such an old path has little hope, we can only find a new path. Just like in the current automotive industry, it is difficult for us to keep up with the engine technology of gasoline powered vehicles in Europe and America, but in the field of new energy, we have repeatedly defeated them.
At the beginning of the sanctions, I was wondering if we had any alternative solutions for chips, as Russia knows how to use transistors as an alternative solution. Therefore, I searched for some information to see if we have similar methods.

The answer obtained after searching around is disappointing, and currently we do not have any alternative solutions. The reason for this problem is that some businessmen once thought that "buying is better than making" was cost-effective, and then everyone followed suit in a crowd.
The current facts have proven that relying on this path cannot go too far, even at risk. Others only need a small card, and we cannot even make high-end phones. I don't know if this is the reason for Zeku's dissolution.
But now there is also a lot of good news. In the field of chips, we are already trying different solutions, and some areas have achieved good results. It is just around the corner to overcome the bottleneck of lithography machines.

one
In the face of sanctions against lithography machines, China has made significant progress in ice engraving technology in recent years. Many experts believe that ice engraving machines are highly likely to replace Western lithography machines in the future, and their advantages are more obvious compared to lithography machines.
Traditional lithography machines require a layer of photoresist to be applied to the wafer before using extreme ultraviolet light to carve electronic circuits. This process has high requirements for the production process of photoresist and requires cleaning after application, making it very difficult to process.
The process of producing chips using an ice engraving machine is similar to that of a lithography machine, with the main difference being the use of ice instead of photoresist. Because ice is formed by changes in water, in a vacuum environment below zero, water quickly forms a flowing ice layer.

The process of applying traditional photoresist on a wafer can be understood as applying glue on a board. The coverage, thickness, and uniformity of the adhesive ultimately affect the quality of the chip.
The ice engraving machine uses an electron beam for carving, and compared to the EUV light source exposure of the lithography machine, the carving process of the ice engraving machine needs to be very meticulous. So the yield of ice engraving machines is higher than that of photolithography machines, but the efficiency is much lower, which is currently a problem that needs to be further solved.
Now the ice engraving process can reach 10nm, although there is still a gap with the latest 3nm lithography machine. However, as long as we stick to this path and have a self-developed heart, there will definitely be opportunities in the future. It should be noted that the polishing of lithography machines in the past also took a lot of time.

two
According to the latest news from technology news, the atomic level transistor technology led by Chinese scientist Zhu Jiadi has also made a breakthrough. This technology uses meteorological precipitation layer by layer stacking technology to produce 1nm or even higher precision chips without the need for a lithography machine, and has lower power consumption.
Because this type of transistor can be made very small in size, the cost of stacking is also lower, but its performance can be more powerful, so this technology achieves higher density integration.
In addition, this technology can also reduce the time required for integration, thereby reducing processing costs.

Don't push, you never know how excellent you are. With the intensification of sanctions, many new technologies are constantly emerging. If this situation continues, I believe that the United States will regret its actions today.
Not only will they no longer be able to hold us back, but it is also possible for their existing business to be split. When we have our own technology, we will no longer buy their products. There is no such a large market in our country, so we will see if they are in a hurry!
Disclaimer: The content of this article is sourced from the internet. The copyright of the text, images, and other materials belongs to the original author. The platform reprints the materials for the purpose of conveying more information. The content of the article is for reference and learning only, and should not be used for commercial purposes. If it infringes on your legitimate rights and interests, please contact us promptly and we will handle it as soon as possible! We respect copyright and are committed to protecting it. Thank you for sharing.(Email:[email protected])